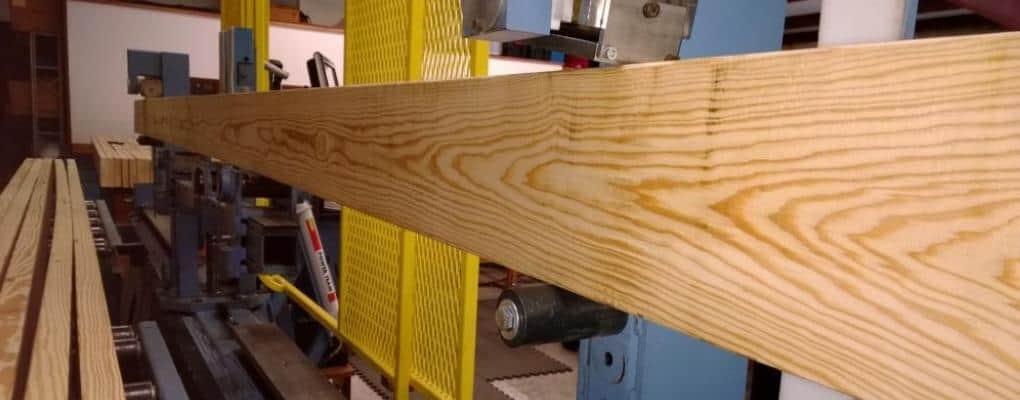
Machine Graded Lumber: Technologies, Quality, and Benefits
For more than 70 years, people have been using machines to assist in the grading of lumber. This article summarizes the machine grading methodologies for producing Machine Stress Rated Lumber (MSR) and Machine Evaluated Lumber (MEL) and highlights the similarities and differences between MSR and MEL. In addition, some structural design benefits from selecting MSR and MEL are presented.
Grading Technologies
When mechanical devices were introduced to North America in the 1960s, they evaluated the stiffness of lumber by observing the load required to cause the deflection of each piece of lumber by a preset amount (see Figure 1). By the 1990s, x-ray technology was developed, whereby variations in lumber density were correlated with strength properties. More recently, acoustic technology has been adapted for use in machine grading of lumber; a sound wave is induced by striking each piece with a hammer and detecting the transmission speed with a microphone so that the speed of sound transmission can be related to the stiffness of the lumber (Additional information on the evolution of machine-graded lumber is available in the USDA Forest Products Laboratory’s GTR 238 Nondestructive Evaluation of Wood, Second Edition). Importantly though, none of these technologies can be used to grade lumber independent from a visual override to ensure overall appearance.
Figure 1. Mechanical stress-rating process. Diagram courtesy of the Western Wood Products Association (WWPA), Technical Guide 4: Machine Stress Rated Lumber.
These technologies — deflection, density, and acoustic — have been implemented in various machines. Currently, there are 34 devices approved by the American Lumber Standard Committee to produce mechanically graded lumber in the United States. Any approved machine may be used to produce either MSR or MEL lumber.
MSR and MEL Production
MSR and MEL are very similar but have a few important distinctions. Both methods use an approved machine to evaluate and sort lumber. Both methods require the application of visual grading rules in addition to evaluation by the machine. Both methods require the producer to “qualify” the grade by testing pieces of lumber to demonstrate that they meet the bending strength (F ) and stiffness requirements for the grade. For structural design purposes, “stiffness” is represented by the Modulus of Elasticity of the lumber, known as “E.”
One distinction between MSR and MEL is that MEL requires qualification testing and daily quality control for strength in tension as well as bending strength and stiffness. Although tension is not one of the daily quality control requirements for MSR, most grading agencies conduct periodic tension testing on MSR lumber to ensure the assigned tension design values are appropriate.
Indeed, both MSR and MEL require daily quality control tests at the producing mill to provide ongoing assurance of the bending strength and E properties. Applying quality technologies and methods for manufacturing MSR and MEL makes a sustainable and environmental resource even more valuable to users.
Design Benefits of MSR and MEL
Both MSR and MEL lumber have lower E-variation than visually graded (VG) lumber. In other words, there is much greater certainty that the E-values for a grade of mechanically graded lumber will vary less than for a grade of VG lumber. For example, Figure 2 depicts the E-variation given an average (grade) E of 1.9 million psi for MSR, MEL, and visually graded lumber (VG). The range of E within a VG (yellow) is substantially greater than the variation for MEL (blue) or MSR (green).
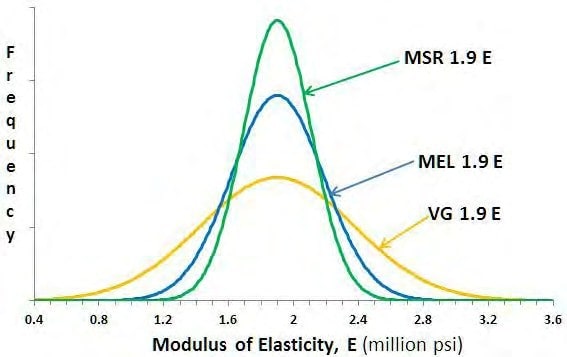
Figure 2. The E-variation resulting from different grading methods. Each grade has an average value of 1.9 E, but the MSR and MEL lumber have substantially less variation from that average.
Statistically speaking, the variation in E for lumber is usually expressed by the “coefficient of variation” or COV. The COV is calculated by dividing the standard deviation by the average E for the grade. Based on the 2018 National Design Specification® (NDS®) for Wood Construction, Appendix F, the COV for VG lumber (without E-sorting during the manufacturing process) is assumed to be 25%. Using the 5th percentile as a benchmark for comparison, the 25% COV yields an expected 5th percentile value equal to 59% of the average E, or 1.12 million psi. The “5th percentile” means 95% of the 1.9E lumber grade would have an E greater than 1.12 million psi.
By using grade thresholds to accept lumber into an MSR grade and performing daily quality control, the COV of E is controlled such that the 5th percentile E value would be 82% of the average or 1.56 million psi for a 1.9E MSR grade. The COV for MEL is controlled such that the 5th percentile E value is 75% of the average or 1.43 million psi for a 1.9E MEL grade. The 5th percentile for MEL is somewhat lower than for MSR but still considerably higher than for a visual grade.
Lower variation in the E values of lumber afforded by MEL and MSR is beneficial in the structural design process as credit is officially given to the products in design equations for beam stability (such as unbraced sections of beams), beam-columns (such as a truss top chords), and columns (such as a wood truss webs). While not officially recognized, solid-sawn joists and floor trusses built with MEL or MSR chords should have a lower differential deflection behavior in-service, a desirable feature for installing hard surface floorings such as ceramic tile and natural stone. Also, the lower deflection variability of MEL and MSR floor framing may improve floor performance with respect to customer satisfaction and generate fewer “soft spots” or similar complaints.
Additional MSR and MEL Design Benefits
In some wood truss applications (such as longer spans) and girders, compression perpendicular-to-grain (FC-perp) stress at bearing locations requires a greater allowable compression perpendicular-to-grain (FC-perp) design value than is available with VG lumber grades. For example, the largest FC-perp for DSS Southern Pine is 660 psi, which may not be adequate in some cases without the use of “bearing blocks” or special metal bearing connectors. Referring to the 2018 NDS Supplement, Table 4C Footnotes, 1.8E (with 0.57 specific gravity, G) and all 1.9E and higher grades have an allowable FC-perp of 805 psi, a 22% increase over DSS Southern Pine.
Assuming the 22% increase in FC-perp is adequate, MSR/MEL can eliminate substantial elevated work of the framing contractor.
Availability of MSR Lumber
While MSR is available in several species across North America, MEL is only produced in Southern Pine. Western agencies have not incorporated MEL procedures into their machine-graded lumber policies. The design values for the published grades of MEL have been optimized to represent property combinations present in the Southern Pine resource. However, other grades could easily be added at any time.
Reading MSR and MEL Grade Marks
MSR can easily be distinguished from MEL by looking at the grade mark. Both grade marks must contain the following information:
- grading agency
- species (which may be represented by the agency name, such as SPIB)
- grade name
- moisture content designation (e.g., KD19 HT)
- a number of the mill producing the lumber (located in an oval)
For MSR products, the phrase “MSR” or “machine rated” must appear, and the grade name consists of two numbers that designate the fiber stress in bending, Fb and the E (e.g., 2400f-2.0E). MSR producers may opt to apply a No.1 grade wane limitation on their MSR, which is designated by the “1W” on the grademark.
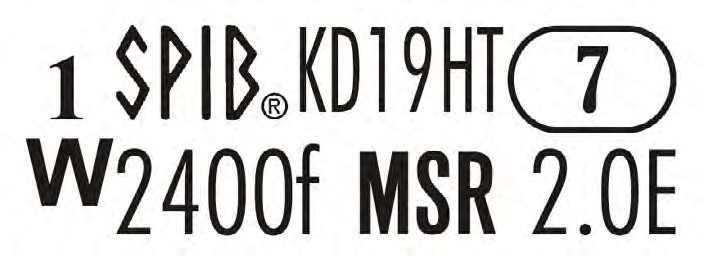
Figure 3. Typical machine stress rated lumber grade mark.
A grade name for MEL is the letter M followed by a number code, e.g., M-9. The grade mark must also show the design values for which quality control is performed, namely bending strength, E, and tension strength.
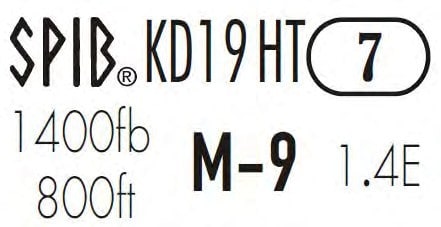
Figure 4. Typical machine evaluated lumber grade mark.
The full range of design values for both MSR and MEL grades can be found in the Southern Pine Inspection Bureau’s Standard Grading Rules and the American Wood Council’s 2018 NDS Supplement.
Concluding Remarks
By cleverly machine sorting the dimension lumber to yield different Fb-E combinations, the end result is more choices for the designer and better utilization of the natural resource. For example, for longer floor truss spans that may be limited by allowable deflection limits, a higher E-grade (for example, 2700f-2.2E) may be ideal. Whereas for pitched roof truss applications where higher strength grades are needed to meet strength requirements, another grade option with higher design strength values (for example, an M-30 grade with 2050f-1.7E) may be the best choice. MSR or MEL lumber can be selected to optimize the use of the wood resource and better match building code requirements for different engineered components and applications, thus enhancing the value of lumber as an environmentally friendly and sustainable material.
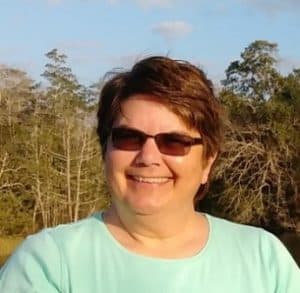
Linda Brown has served as the engineer for the Southern Pine Inspection Bureau for over twenty years. Her primary responsibilities include SPIB’s continuing Resource Monitoring Program and the Mechanically Graded Lumber Program. She is active in ASTM as the Section Chair for D07.02.01 Solid Sawn Lumber and serves as an advisory member on the American Wood Council’s various standards committees. Comments are welcome and can be sent to lsbrown@spib.org.
Frank Woeste, P.E., is Professor Emeritus, Virginia Tech and a wood construction consultant. Frank, along with his colleagues, has developed and presented continuing education programs for more than 30 years. He is a member of the ANSI/TPI 1 Project Committee for revision of the truss design standard and the AWC Wood Design Standards Committee, and serves as the Consumer Representative (Alternate) of the ALSC. Comments are welcome and can be sent to fwoeste@vt.edu.